EHEDG Certification for Fork Level Sensor
By Dhananjay Palshikar on May 3, 2019
BeginnerHygienic Design of Level Sensors
Maintainance of hygiene in Food and Drug industries is critical to a plant's operation. Use of a non-compliant equipment or a non-compliant cleaning process can lead to health and safety risks for consumers.
The primary goal of hygienic design is to ensure validity of efficient sanitation processes. In other words, if an equipment with hygienic design is used, efficient clean-in-place methods should be considered valid in order to ensure hygiene.
EHEDG Certified Level Sensors
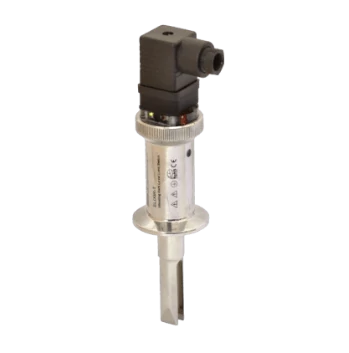
Regulartory Environment for Hygienic Equipments
Regulatory bodies such as FDA(Food and Drug Authority) in United States have laid down standards and good practices for manufacturing.
EHEDG: European Hygienic and Design Group is not a regulatory body but a consortium of companies devoted to the advancement of hygienic design and food engineering.
FSSAI(Food Safety and Standards Authority of India) in last few years has been increasingly active in promoting hygiene amongst business involved in food products. A license regulation has been released. The documents covers all aspects of hygiene. However details on equipment hygiene or hygienic design are limited.
With the advent of Mega Food Parks in India, the shift to globally recognized manufacturing practices will be the way forward. Therefore, even if hygiene regulation for equipments in India is still catching with internationally accepted practices, the norms accepted by FDA and EHEDG would naturally apply for export of edible processed goods.
Why hygienic design matters for a level sensor?
- Buildup of application media and Bacterial growth
- Pipe Fittings and Mounting Arrangements
Level sensors based vibronic or capacitive principles are directly in contact with the application media. Even with free-flowing liquids some build up is expected. If not specially designed, application media particles get deposited on the surface and crevices of the level sensor.
If left uncleaned, these pockets of particles can act as breeding grounds for bacteria. e.g. In dairy plants, this could lead to curdling of the entire batch of raw milk. In pharmaceutical plants, such incidents can put consumers at risk.
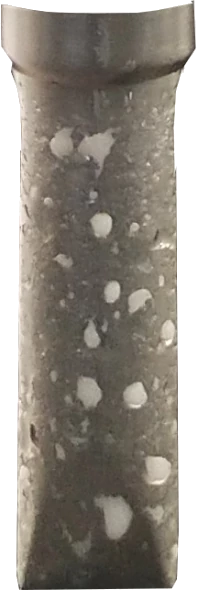
Mounting arrangement may come in contact with the application media, irrespective of the the principle of level measurement. Crevices created by threads or joints between two surfaces provide area for bacterial growth.
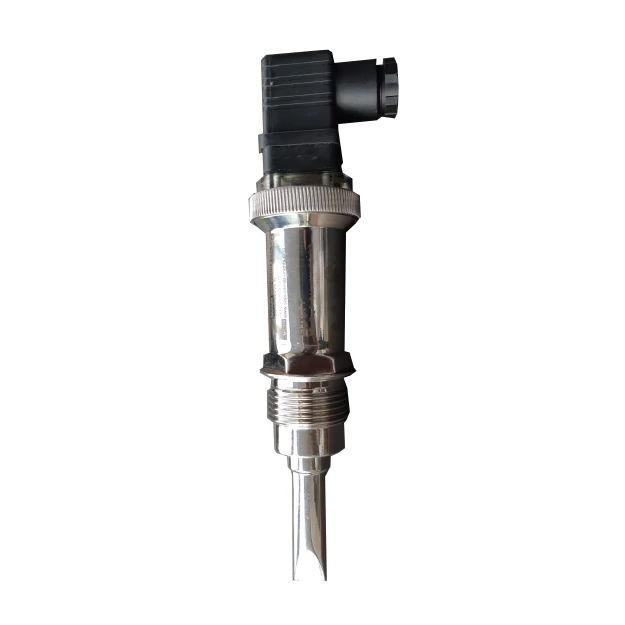
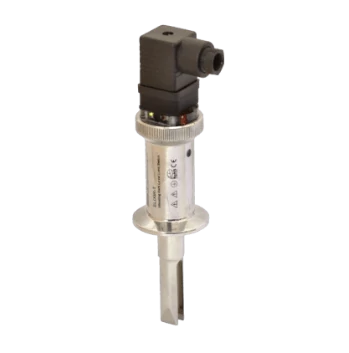
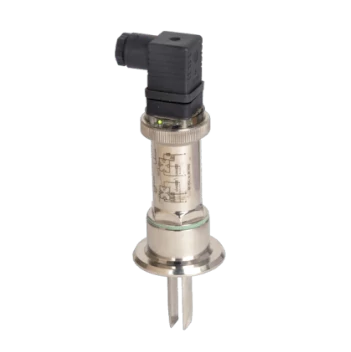
Hygienic Design for a level sensor
While each level sensor variant has to qualify certification individually, the guiding principles for design are similar. For more detailed understanding refer to EHEDG Free Documents. Primary design and manufacturing criteria considered by Sapcon Instruments have been briefly explained below.
- Selecting Material of Construction
- Inhert to application media, cleaning detergents and disinfectants
- Corrosion resistant
- Non-toxic
- Non-tainting
- Mechanically stable
- Standardization of Manufacturing Process
- Geometry Considerations
- Importance of Surface finish
- Hygienic Pipe Fittings for level sensors
Level Sensors used in hygienic applications are primarily made of SS316 grade stainless steel. EHEDG in its document specifies the following criteria for selecting materials:
Material such as Plastics, Glass, Ceramic may be used under certain conditions. Devices such as Pressure Transmitters must use non-toxic signal-transfer liquids.
Although, EHEDG does not mandate a process qualification for manufacturing; standardization and qualification of the manufacturing process can help ensure sustainable quality.
The surface geometry of level sensors may have a curves, acute angles and crevices in a way which could lead to deposition of food particles. If such surfaces are unavoidable in the sensor, then the product needs to go through a hygienic evaluation test.
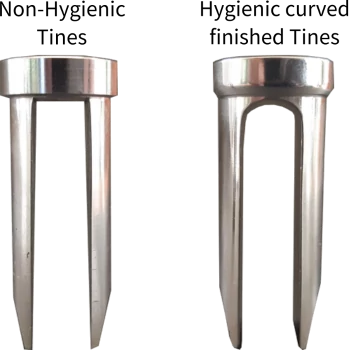
EHEDG recommends a Surface Roughness Average of 0.8 µm for the surface of the level sensor in contact with the application media.
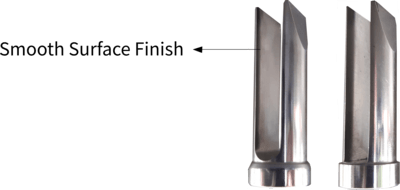
EHEDG releases its approved set of pipe fittings periodically. Using standard pipe fittings has the benefit of being compatible with several makes of level sensors. Some manufacturers of level sensors offer EHEDG approved pipe fittings which have been customized for their make. This can cause vendor-lockin issues when looking for replacement.
EHEDG Certfication Types and Classes
- EL: Equipment cleaned with liquids
- ED: Equipment dry cleaned only
More articles on Certifications