Rotating Paddle Level Sensor
By Dhananjay Palshikar on May 17, 2019
IntermediateIntroduction
Predecessor to all level sensors, Rotating Paddle was first introduced in 1950s. It is the original level sensor, and has left its mark on product descriptions even today. The best anectodal evidence can be seen in the salient features of Vibrating Fork Level Sensor; the line "No moving parts" is included in several makes of Vibrating Forks across countries.
Like most first innovations, designers of the Rotating Paddle Level Sensor used a seemingly simple principle in a very effective manner, such that a variety of application materials could be covered, with minimal adjustments.
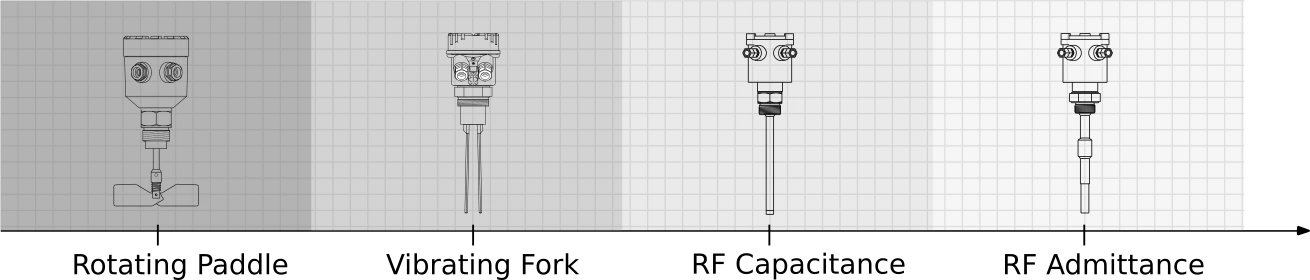
However, newer level sensors technologies based on Vibrating Tuning Forks, RF-Capacitance and RF-Admittance were being introduced since 1970s; these had one major advantage:
Life Span
The useful life of competing level sensor technologies was significantly higher as compared to Rotating Paddle Level Sensors.
Over the next few sections, an attempt is made at briefly describing aspects of Rotating Paddle Level Sensor that could be relevant while choosing it over other level sensor. Companies manufacturing rotating paddle level sensor now making it with several variations.
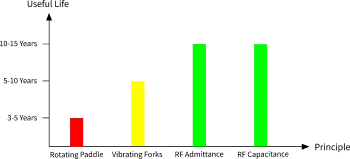
Principle
An electric motor drives the shaft connected to the rotating paddle. The twin blades of rotating paddle rotate freely when uncovered. The electric motor is mounted on a sliding-fit rotating disc, which in-turn is connected to a spring. When rotating freely, the spring is relaxed, as the application media covers the blades of the rotating paddle, the torque requirement increases, which extends spring. The spring extension is detected by position sensors, thus level of application media is detected. The power to the motor turned off. Subsequently, when the rotating paddle is uncovered, the spring ensures the motor is back to the position where motor can be powered on.
Driving Mechanism: Electric Motor
Based on the torque requirement and availability of space motors used in Rotating Paddle could be one of : DC Synchronous Motor, AC synhronous motor, Stepper motor.
Servo motors have not been considered as no known manufacturer is known to be using it. Although, a servo motor could make an interesting choice, more on that later. Based on low input power supply, long useful life of 3 years and the possibility of adjusting speed and torque of motor makes DC gear stepper motor emerge as the best option.
Input Power Supply
While most other types of level sensors have upgraded to AC-DC wide range universal power supply, Rotating Paddle Level Sensor in most cases continue to be available in separate AC powered and DC powered models.
The choice of motor determines the required power supply. For DC motors SMPS power supplies can step down a wide range of voltage to the desired 5V/12V. For 230V/110V AC powered motors, it is expensive the step up the voltage efficiently for low voltage DC input. Also generating a sine wave from DC votlage is non-trivial and therefore not used.
Sapcon's Rotating Paddle: Orbit, has a wide range AC-DC(18-265 AC/DC) power supply which is very rare in the industry.
Sensing Mechanism
- Placement of motor
- Position Sensing devices
Generally when the rotating paddle is covered with application media, the rotational motion faces resistance. At this point, the torque applied by the motor rotates the sliding disc instead of the rotating blade.
Instead of a circular disc an alternative arrangement of a chasis can also be used to achive the same result. Here the motor can often have an off-center shaft.
The power to the motor is cut-off based on the signal from the position sensing device, the position of the motor itself or the peripheral beacon attached to the motor is sensed. The position sensing device plays an important role in determining useful life of the rotating paddle level sensor.
Micro-switches
Microswitches are simple devices which can be actuated by very little physical force. Due their mechanical operation wear and tear with time is possible.
Reed Switches
Magnetically actuated, non-polar, low cost switches. These are however not immune to mechanical damage.
Hall Effect Sensors
Solid State semi-conductor devices, can be more expensive, but can have a much longer useful life.
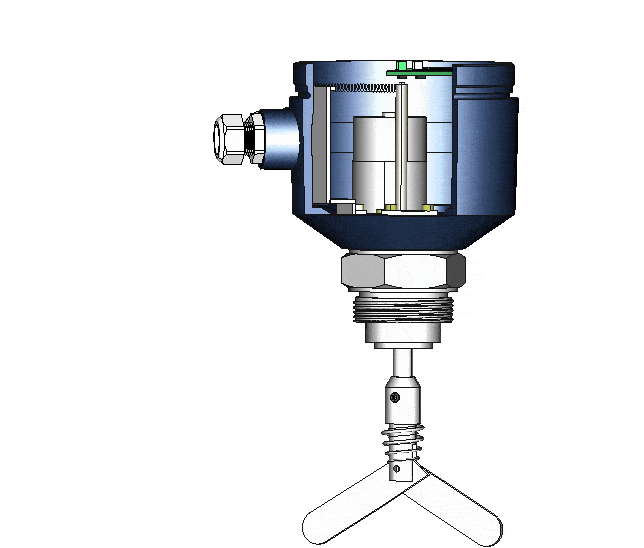
Ability to change motor RPM (Rotation per Minute)New Feature
This feature introduced by Sapcon Instruments is particularly unique. Stepper motors can make adjustable RPM possible. With a higher RPM, lower tourque is expected, while with lower RPM higher torque output is expected from the motor.
With an onboard micro-controller, intelligent speed adjustment can be used to significantly reduce the response time with long rope type paddle level sensor
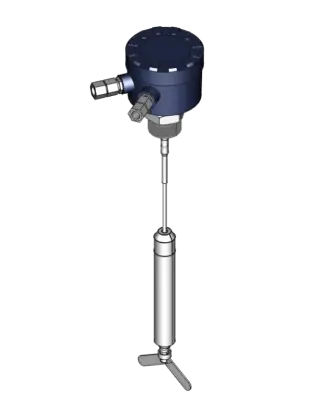
Sensitivity Adjustment
Sensitivity adjustment may be required to sense low density application media. At a lower torque setting is useful for low density media. This is typically done by adjusting the spring.
Design of Paddle Blades
More surface area can provide more traction with application media, this is used in detecting low density application media like plastic chips.
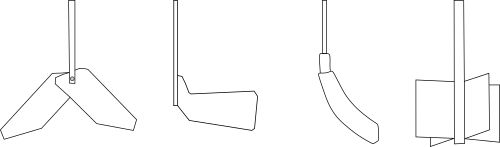
Output Mechanism
Low cost solution often use microswitches as sensing as well as output devices. Sapcon instead uses standard 10A rated DPDT relays, hence making the choice of power supply more flexible.
Safety: Microcontoller controlled relay outputs makes the Failsafe operation of Rotating Paddle Level sensor independent of mechanical failures.
Factors affecting performance and useful life
Rotating Paddle is in-famous for the afore-mentioned mechanical wear and tear. An empirical analysis of site conditions has revealed the more factors, some of which can be avoided by proper installation and maintainance.
- Wear-and-tear due to motion
- Ingress of dust
- Buildup of application media
- Visually verifiable mechanism: Understanding the principle by seeing the sensor in operation can instill more confidence, as the mechanism of rotating paddle level seems obvious even to modestly trained operators on the shop floor.
- Pre-installed; Replacement buys: Most rotating paddle sensors are replacement buys, the rotating paddle sensors have been around long enough to have been replaced a few times. In such cases going for a familiar option seems a less risky option.
- Immutable Purchase Specs: The specifications may be frozen by a third party consultant, all that the buyer has a choice is to select the make.
- Attractive low cost options: As seen above, manufacturers can make a choice to use low cost components and reduce their raw material cost. A combination AC Synchronous motor, single power supply option(only AC) and micro-switch ouputs can make a compelling buy. However the lack of features accompanied with low cost substitutes for bearings, motor, oil-seals, PTFE bushes the useful life of the paddle level sensor may be affected.
- Testing New Application Media: Unlike RF-Capacitance and RF-Admittance only physical parameters like specific gravity, particle size of the solid need to be known. A trial over a short duration of a day can be fairly conclusive in determining the success of the paddle level sensor in a particular application media.
- Benchmarking against international products
- Proof of concept for individual modules
- Iterative Design:Only the best one makes it to production
- Extensive in-house testing
- Process qualification design for production
Electric motor, ball bearings, oil-seals and PTFE bushes are primarily affected by rotational motion. As time progresses the frictional force is bound degrade the performance, however for most applications, the cost of Rotating Paddle Sensors would be recovered towards the end the of the useful life of the level sensor.
Dust ingress can be avoided by correctly installing and maintaining the cable glands. Dust can increase the friction between moving parts in the instrument. This may lead to fast wear-and-tear of the instrument.
For hygroscopic media or media that has a tendancy to stick on the level sensor; Rotating Paddle Level Sensor is not recommended in such application media.
Incorrect horizontal mounting arrangement
For horizontally mounted low level sensor, the load on the probe may result in misalignment of the shaft if baffle is not installed above the low level sensor. Misalignment of shaft may lead to an excess pressure on the motor, reducing the useful life of the instrument.
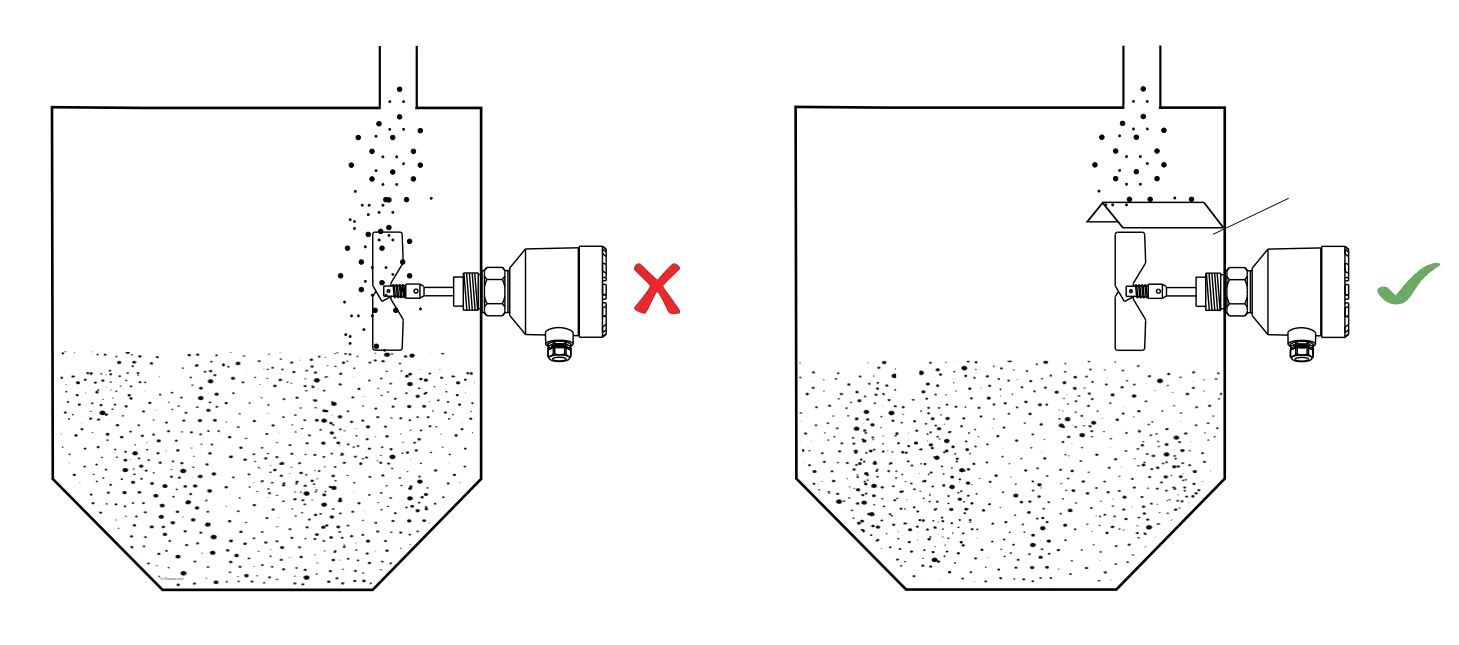
Why Rotating Paddle Level Sensor is the preferred choice for many buyers
Apart from emperical performance on the plant shop-floor, there are other factors that instill confidence in the typical buyer of a rotating paddle level sensor. The following factors are important to list as an acknowledgment of these factors may help a buyer reconsider or re-inforce Rotating Paddle Level sensor as the first choice.
How Sapcon is addressing limitations of Rotating Paddle Level Sensor
The natural generational changes have brought in important to corrections on previous designs.
More articles on Intro Level Sensor